Austin Construction Company for Dummies
Table of ContentsAce Construction Company Austin Can Be Fun For AnyoneAustin Construction Company for BeginnersFacts About Ace Construction Company Austin UncoveredThe Ultimate Guide To Construction Company AustinNot known Details About Ace Construction Company Austin The Best Strategy To Use For Construction Company Austin
But prior to that, here are some key concerns to think about. More than problem-solvers, maintaining walls also have a sculptural quality that adds meaning to the landscape, and they can be made from numerous materials to evoke various designs. Stacked woods or mortared stone, for instance, can impart a rustic look, while put concrete is sleekly contemporary.
How effective your wall will be and how long it'll lastdecades or just a few yearsdepends largely on things you can't see, such as a sound footing buried in the ground and drain to keep water from constructing up behind the wall. Prices start at $4. 30 per square foot for put concrete, $5.
15 for pressure-treated pine, and about $11 for stone - austin construction company. Installation or supplies, such as drain stone or filter material, are not consisted of. Lumber can last up to 40 years; there's no limit on the life span of an appropriately set up masonry or concrete wall. Timber and inter-locking-concrete-block walls are terrific DIY maintaining wall ideas.
Codes mandate that walls greater than 4 feet high be created by an engineer and built by an expert. Besides an occasional clearing of the weep holes, keeping walls do not require much attention. The fundamental parts of a mortared-stone wall. Elements can vary for other types of retaining walls.
Getting My Austin Construction Company To Work
These walls need only a standard crushed stone footing and T-shaped wood deadmen to anchor them. Pressure-treated pine and fir that are rated for ground contact need to survive 40 years; western red cedar or redwood lasts about 20. Pressure-treated pine, $6. 15 per square foot uninstalled; Lowe's With enough drainage, stone, brick, or concrete-block walls are strong and long-term.
Mortared walls rest on a rebar-reinforced concrete footing set listed below the frost line and require weep holes to ease soil pressure. Mortar-free dry-stacked stone retaining walls need just a crushed-stone footing. Cost: Fieldstone, $11 per square foot uninstalled; The Stoneyard The strongest and most resilient option, concrete can be marked, stained, veneered, or carved to appear like mortared stone.
Leave the style, formwork, and pouring to professionals. Like mortared masonry, these walls are supported by an enhanced concrete footing and need weep holes. This is the only wall type that isn't battered (leaned back) versus the earth. Ready-mix from a truck, $4. 30 per square foot uninstalled; C & C Ready-Mix Corporation An easy choice for DIYers since of their light weight, flat sides, and the sure-fire method they fit together without mortar.
Like timber and dry-stacked stone walls, they rest on a crushed-stone footing. Durable mesh anchors every other course against the ground. Versa-lok Weathered Mosaic (shown), $11. 40 per square foot uninstalled; Versa-Lok Reader Mike Sieber of Mannington, West Virginia, stacked big stone modular blocks to level off a steep decline and make distinct areas for amusing and game-playing.
Things about Construction Company Austin
Reader Sandra Yoshioka of Torrance, California, used stuccoed-block walls to produce a flower-filled buffer between the pathway and her front door (construction company austin). Reader Clifford Parker of Jamestown, California, raised the grade in his yard and constructed a hybrid stone-and-timber wall to hold up the external edge of a new gravel drive.
Water-based spots can be used with a sprayer or roller straight onto a clean, unsealed surface. Rust-Oleum concrete stain, 15 cents per square foot. Smooth away the blahs, and any surface blemishes, with a coat of cement-based stucco. When tinted or painted an earthy shade, stucco will also match your landscape.
To perk up a boring surface, adhere thin pieces of brick or stone, or concrete molded to simulate stone or brick. You get a conventional search for less than the expense of routine mortared masonry. Natural Stone Veneers, Tuscan Collection, beginning at $8 per square foot uninstalled. "Can My Wall Be Conserved?" Just a structural engineer or mason can state for sure, however if yours programs any of these signs, it might be time for a brand-new one.
Whether it's triggered by tree roots, bad drain, or a stopped working footing, a leaning wall will probably need to be destroyed and restored from scratch. You can fill small imperfections in put concrete with hydraulic cement. In a mortared wall, merely chisel out harmed joint filler and repoint. However if the fractures are more than -inch large and deep, and more than 2 feet long, the wall might have structural damage.
8 Simple Techniques For Austin Construction Company
A noticable dip in the courses of a lumber or interlocking block wall suggests that the footing has failed in one area. A pro might have the ability to change the footing beneath the damaged location and reconstruct just that area of the wall. When mortared masonry establishes a pot stubborn belly, the most likely culprit is an accumulation of water pressure behind it.
A bulge in a description lumber or interlocking block wall is normally official statement triggered by a lack of anchoring. Careful excavation behind the wall might permit a protruding area to be restored. Speak with a professional before beginning work. Trying to find a vegetative wall design? Use plants to soften a rugged expanse of masonry. They can be spaced to develop spaces, parking areas, handball courts or any other functional space. Utilize your creativity! Keeping Walls - Books & Publications CLICK THE IMAGE to see a broad selection of books and guides on how to construct, drain, and design retaining walls. Column B37.
When creating a retaining wall, there are seven elements to think about: products, kind of wall, design or on-site placement, drain, structures, cant or batter, and anchors or "deadmen". When picking products, pick the type that is finest matched for the required outcome. Lots of long-lasting products are offered for landscape use including flagstone rock, recycled concrete paving dealt with timbers, vertical poles, precast concrete modular systems, put concrete, and brick veneer.
Decide if you require a poured-in-place concrete "structural" wall or a much less costly "dry-laid wall" including stacked, open-joint material. Planning ahead will help you avoid the expense and time it requires to transfer a wall or to modify maintained areas once they're installed. Many keeping walls fail due to the fact that of pressure versus the wall triggered by water or soil-moisture develop up behind the wall.
Our Austin Construction Company Diaries
This is achieved with gravel backfill, or manufactured drain blankets and drain pipelines. Structural walls need "weep" holes to permit water to drain from behind the wall. A wall is only as great as its foundation and all retaining walls need to be developed on structurally sound, compacted foundation sub-base product.

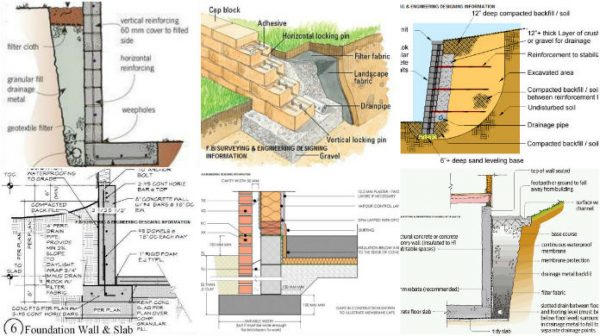
Set up wall expenses usually vary from $20 to $35 per square foot of wall face for dry-laid materials. Cost will vary significantly depending on materials utilized and general wall height. Structural wall expenses might range from two to ten times that of dry-laid walls.
The Greatest Guide To Ace Construction Company Austin
Mechanically Supported Earth Retaining Wall The weather condition is starting to warm up. The nights are still cold, however the days are ending up being warmer. We are aware that spring is in the way. At Kahn Engineering, we are thinking of retaining wall styles. In fact we have actually already created 3 keeping walls this year and remain in the procedure of developing two more.
This type of retaining wall relies heavily on the ability of the stem and footing to keep back the maintained soil. This kind of retaining wall is among the more expensive maintaining walls due to the large excavation expenses and huge quantities of concrete. Even here, there are applications where this type is the very best for the conditions.
The footing is excavated and put in the traditional method, and then the vertical part of the keeping wall is attached to the footing. This again is a more pricey way to construct a retaining wall, however definitely does have it applications in taller walls. Sheet Piling Retaining Wall You will frequently discover sheet stacking around ports near the ocean.
The "sheet" is often rippled or corrugated to have the biggest quantity of strength in minute. These have been used in long-term scenarios, although a lot of engineering documentation suggests that these be used in temporary circumstances. A Buttress shows up or in front of the maintaining wall, while the Counterfort is not visible or behind the maintaining wall.